Inspection in Circus Rigging
We all recognise regular inspections are needed for aerial rigging equipment in circus. This article is designed to help answer the questions:
- What do we need to inspect?
- How often do we need to inspect it?
- What types of inspection should we perform?
- What does the law say?
All equipment
Generally speaking we can say the following about any circus equipment
- What do we need to inspect? You must inspect any work equipment that creates a significant risk when it's in use
- When should we inspect? As often as is necessary to ensure the equipment is safe to use. This starts upon initial installation and includes any subsequent re-installation where there are any conditions that could lead to the equipment being damaged, or could affect safe use.
- Who can inspect? A 'competent person'. That is, someone who has the training, knowledge and experience to perform the required inspection.
- How do we define "what" and "when" for our use? It’s up to the employer to make a risk assessment and set out their policies and procedures accordingly. That applies to the self-employed too.
- What are the reporting requirements? The records you need to keep, how long you keep them, who may need to see them and when that may happen, are factors that will vary depending on which regulation applies.
What laws can apply to circus equipment?
The four laws we need to look into to determine what inspections are needed for our purposes:
- Provision and Use of Work Equipment Regulations 1998 (PUWER)
- Personal Protective Equipment at Work Regulations 1992 (PPEW)
- Lifting Operations and Lifting Equipment Regulations 1998 (LOLER)
- Working at Height Regulations 2005 (WAH)
PUWER covers all work equipment unless there is a regulation designed to cover more specific types of equipment. All of the regulations after PUWER that we are referring to in this article are relating to specific types of equipment. PUWER is usually the minimum requirement. If you are complying with the more specific regulation (LOLER, WAH, PPEW) then you are also likely complying with PUWER.
PPEW covers Personal Protective Equipment (PPE) such as that used in work restraint and fall protection. This typically includes equipment such as harnesses, climbing slings and karabiners but could include anything regarded as PPE.
LOLER covers equipment that is used in lifting operations and has specific, stringent guidelines about equipment used for lifting people.
WAH covers equipment to protect people while working at height. Let's have a look at each regulation in turn.
PUWER 1998 Requirements
In PUWER the term 'work equipment' covers any machinery, appliance, apparatus, tool or installation for use at work. This includes equipment which employees provide for their own use at work. So the scope of PUWER is therefore extremely wide.
PUWER places the burden on the employer to ensure equipment is fit for purpose and to take into account the risks to health and safety of people in the premises. The decision on what and when to inspect would therefore be determined through performing a risk assessment.
PUWER states that:
"where the safety of work equipment depends on the installation conditions, it is inspected to ensure correct installation and that it is safe to use."
The frequency of the inspection would also be determined by the risk assessment
"to ensure that health and safety conditions are maintained and that any deterioration can be detected and remedied in good time."
Reporting requirements - With regards to record-keeping
"Every employer shall ensure that the result of an inspection made under this regulation is recorded and kept until the next inspection under this regulation is recorded."
The actual inspection can generally be done by an in-house employee with an...
"adequate knowledge of the equipment to:
- (a) enable them to know what to look at (know the key components);
- (b) know what to look for (fault-finding);
- (c) know what to do (reporting faults, making a record, who to report to).
Lifting Operations and Lifting Equipment Regulations 1998 (LOLER)
LOLER governs equipment that is used for lifting. This would include anything from goods used in construction being lifted by a crane to a performer being lifted by a pulley system. This would not include equipment like static trapeze or flying trapeze unless the equipment itself was being lifted.
Who can inspect?
The person carrying out the inspection can be an in-house employee. However, the employer must ensure that person has:
"the genuine authority and independence to ensure that examinations are properly carried out and that the necessary recommendations arising from them are made without fear or favour."
The person carrying out the thorough inspection should also not be the same person who performs the routine maintenance.
"This is to ensure that there is independence between the thorough examination and the maintenance and to avoid an individual examining their own work. When these functions are carried out by different people, the additional safety aspect of having a second person checking the equipment makes it more likely that defects will be identified and rectified."
"Where the thorough examination is undertaken by the same person who has maintained the equipment, your risk assessment should show you have considered all the options, how you reached your decision about who should carry out these functions, and also show that the person is suitably qualified and independent to the extent that would be required for another competent person.
How to inspect?
The following section of the regulations refers to 'scheme' by which they mean process or method of examination:
"Any examination scheme for lifting equipment should take account of:
(a) its condition;
(b) the environment in which it is to be used; and
(c) the number of lifting operations and the loads lifted.
The legislation includes the following paragraph stating that your policy procedure does not need to be written. However, having a written document is the sensible way to ensure the other aspects of that paragraph: that it can be produced in writing if required, and that the procedure is not open to unauthorised modification. You will need written records of inspections so you might as well keep your policy and records together.
The examination scheme need not necessarily be preserved in the form of a document. It should, however, be capable of being reproduced as a written copy when required. It should be secure from loss or unauthorised modification and it should be authenticated by the competent person preparing the scheme."
How frequently should we inspect?
LOLER mandates that equipment used for lifting people should be inspected, through a thorough examination, at least every six months.
What are the reporting requirements?
LOLER requires the results of an inspection to be recorded in a Report of Thorough Examination. In contrast to PUWER, the record must contain particulars that the LOLER regulations specify in Schedule 1. A copy of schedule 1 can be found at the end of this article.
The Personal Protective Equipment at Work Regulations 1992 (PPEW)
PPEW is designed for Personal Protective Equipment (PPE) being used as PPE. If that same equipment is being used in a lifting operation, then LOLER will need to be applied.
How frequently should we inspect? PPEW states that inspections should be conducted according to manufacturers' guidelines.
What are the recording requirements? Defects are to be reported to the employer and the report should be kept until the next inspection or for a period of 3 months, whichever is longer. The person carrying out an inspection of work equipment must provide a written report before the end of the same working day and a copy must be kept at the site where the inspection was carried out until the construction work is completed.
Working at Height Regulations 2005 (WAH 2005)
WAH has very similar inspection requirements to PUWER; the difference is that WAH states that inspection to protective equipment should be done 'in place'. What this means is that we are not disassembling the protective systems, but inspecting them 'in situ'.
Circus scenarios
So which regulation applies to us and under what circumstances?
Access equipment
If we are using equipment as PPE and using it to access the rigging, then PPEW will apply unless a lifting operation is involved.
Suspended equipment
If you are purely suspending equipment such as static trapeze, hoop, silks from a truss or eyebolt, PUWER would apply so you would simply need evidence that you inspected the round sling, karabiner, fabric, figure 8 or silk etc. You would need to keep that document until the next inspection.
You will also need to produce this documentation declaring that your equipment is safe for use if you use your equipment in premises other than your own, or if you provide that equipment for others to use – for example, if you run classes, or if you lend your equipment to someone else.
Flying and lifting equipment
If the equipment in question is lifting someone, for instance a performer on aerial hoop, then LOLER applies and the rules change.
Whether you are using a human counterweight, hauling up a person by a rope over pulleys, or with a winch or hoist, it would be subject to LOLER 1998.
The same karabiner, figure of 8, silk, straps or hoop previously used under PUWER are now connecting a human load to lifting equipment. Lifting people, quite possibly at high speed, creates risks that are quite unique.
The requirement in LOLER 1998 is for a 'Thorough Examination' of such equipment in addition to any inspections. Like PUWER, the equipment has to be inventoried and declared safe to use. The employer must appoint the competent person(s) to carry out the thorough examination. The competent person then becomes responsible to the employer for determining the frequency, nature and level of detail of the thorough examination, and ensuring that it is appropriate for the equipment and its use.
Visual inspection vs thorough examination
As the use of the lifting equipment is to lift people rather than goods, the need for a thorough examination rather than a visual inspection should be clear. In practice, an inspection under PUWER could look very much like a LOLER thorough examination.
The risk assessment will determine what the PUWER inspection actually involves. It could range from a visual inspection to a thorough examination including load testing.
The competent person
The 'competent person' in this context is best defined as someone with the appropriate blend of knowledge, skill and experience for the task in hand. There is no legal definition so common sense must be applied.
The competence to inspect circus equipment such as a silk or corde lisse would definitely require detailed knowledge of the materials, their use, the manufacturer’s information and, crucially, experience of doing inspections or thorough examinations of the equipment in question.
In the event of an equipment failure, if the person conducting the inspection was not competent in that piece of equipment, they would have to accept some or all of the responsibility for the consequences, which could be injury or loss of life.
Clearly, gaining training for the safety of all your equipment is important, and it is the employer’s duty to provide appropriate training to employees. That can sometimes be achieved in programmes offered by some lifting equipment manufacturers, or the employer may operate an in-house programme with someone who has already been proven competent.
All training should be documented and efforts should be made to stay up to date.
If you are intending to inspect purpose-built equipment, which is not uncommon in the world of circus, it would be wise to check if it was supplied with a manual (it should have been!). Either way, ideally the person who made it should train people to inspect it.
How do you know if you are competent to inspect? Two often-quoted phrases:
- “If you need to ask if you’re competent, you’re probably not.”
- “If you could train someone to do something you’re probably competent in that task”.
There is no requirement in the UK for specific qualifications etc, other than being competent for statutory or pre-use checks. The duty to ensure that inspection happens and a competent person is employed to do so is placed on the employer.
When to use a third party to do the inspections
Legally, the duty to inspect falls on the employer or self-employed person who must ensure a competent person plans the nature, frequency and extent of inspections. For years in the UK, the Health and Safety Executive (HSE) have advocated using people within an organisation over an outside body because those closest to the work often know the equipment and risks the best.
Where the competence is lacking (partially or wholly) you would need to use a third party, unless your insurance company has more onerous conditions. Inspecting slings and karabiners, silks, hammocks and corde lisses etc is probably well within the competence of most teachers, performers and studio owners.
Pulleys and other equipment such as a Petzl Rig or ID may be more challenging, but many users will be able to carry out an inspection if they have access to the manufacturer’s information and maybe a few simple measuring tools.
If the equipment comprises of lines and pulleys, descenders or belay devices and the like, someone who is competent in inspecting such equipment is needed. That person may well be someone with aerial rigging or rope access experience. If the equipment involves a winch or hoist (since we borrow so much proprietary gear used by other industries) you may need to hire someone who can strip down, examine, rebuild and test the machine.
It's often the case that a bona fide qualified industrial lifting engineer will have no experience of a lifting system made from ropes and mountaineering pulleys. They might even condemn it (wrongly) as not 'legal' for lifting people, whereas an aerial rigger will have no doubts about 'signing it off'.
By the same token, an aerial rigger rarely has the necessary competence to carry out a thorough examination on a wire rope winch to the level of detail required by the regulations.
There is need for a joint approach in such cases, and what is required would be determined by the risk assessment.
Manufacturer information and a caveat
It’s been law in the UK since 1974 (Section 6.3 of HSAWA) that manufacturers and suppliers must provide the information required to use their product safely (even if we don’t read it!). Providing full instructions and information with their product is the manufacturer’s obligation, making sure they stay safe to use is the employer’s obligation (EU/UK).
Good quality equipment comes with paperwork. If it doesn’t it is either because it may not of good quality or more likely it wasn’t designed for what you are using it. A figure 8 is a great example, the manufacturers never mentions aerial silks in their instructions but will always tell you only to use it in accordance with their instructions. Therefore the user takes the responsibility for safe use of the product and effectively absolves the manufacturer from any liability.
Thoughts on inspection in circus LOLER vs PUWER
What if you have equipment that is used for suspending circus equipment and other equipment for lifting? If you can clearly show that you have a firewall between the two areas of practice and separate equipment, then you can apply separate inspection regimes. This would need to be reflected in the risk assessments, method statements and staff training.
Is there any difference in the type of inspection needed under PUWER and the thorough inspection under LOLER? The nature of the inspection is likely to be very similar to what a Thorough Examination required by LOLER and if the risk assessment determines a 6 monthly frequency of inspection then the PUWER protections look very much like LOLER.
What are the benefits to being able to apply PUWER for those with small studios or training spaces where the equipment is only suspended? If the inspection and frequency is likely to be the same as those performed under LOLER; the main benefit is that you wouldn't be legally required to bring in a third party to perform the inspection. In addition the details in the report for each item is very specific under LOLER and contains 11 pieces of data. The risk assessment under PUWER may determine that less information is needed.
Exceptional circumstances
There may be a valid reason that we can't apply LOLER regulations as written. We could therefore create a written scheme which changes the inspection frequency but it must be justified and documented. You may want to look at it from the perspective that you may one day have to justify that decision in court.
In the case of an exceptional event occurring such as the equipment being overloaded or being exposed to harmful environments or activities then an inspection (PUWER) / thorough examination (LOLER) would be required following that event.
The information to be contained in a report of a thorough examination under LOLER
The following is a direct copy from the regulations as to what information is needed in a report of thorough examination:
1. The name and address of the employer for whom the thorough examination was made.
2. The address of the premises at which the thorough examination was made.
3. Particulars sufficient to identify the lifting equipment including where known its date of manufacture.
4. The date of the last thorough examination.
5. The safe working load of the lifting equipment or (where its safe working load depends on the configuration of the lifting equipment) its safe working load for the last configuration in which it was thoroughly examined.
6. In relation to the first thorough examination of lifting equipment after installation or after assembly at a new site or in a new location
(a)that it is such thorough examination;
(b)(if such be the case) that it has been installed correctly and would be safe to operate.
7. In relation to a thorough examination of lifting equipment other than a thorough examination to which paragraph 6 relates—
(a)whether it is a thorough examination—
(i)within an interval of 6 months under regulation 9(3)(a)(i);
(ii)within an interval of 12 months under regulation 9(3)(a)(ii);
(iii)in accordance with an examination scheme under regulation 9(3)(a)(iii); or
(iv)after the occurrence of exceptional circumstances under regulation 9(3)(a)(iv);
(b)(if such be the case) that the lifting equipment would be safe to operate.
8. In relation to every thorough examination of lifting equipment—
(a)identification of any part found to have a defect which is or could become a danger to persons, and a description of the defect;
(b)particulars of any repair, renewal or alteration required to remedy a defect found to be a danger to persons;
(c)in the case of a defect which is not yet but could become a danger to persons—
(i)the time by which it could become such danger;
(ii)particulars of any repair, renewal or alteration required to remedy it;
(d)the latest date by which the next thorough examination must be carried out;
(e)where the thorough examination included testing, particulars of any test;
(f)the date of the thorough examination.
9. The name, address and qualifications of the person making the report; that he is self-employed or, if employed, the name and address of his employer.
10. The name and address of a person signing or authenticating the report on behalf of its author.
11. The date of the report.
References
- Provision and Use of Work Equipment Regulation 1998
- Lifting Operations and Lifting Equipment Regulations 1998
- The Personal Protective Equipment at Work Regulations 1992
- Working at Height Regulations 2005
In partnership with Articulation
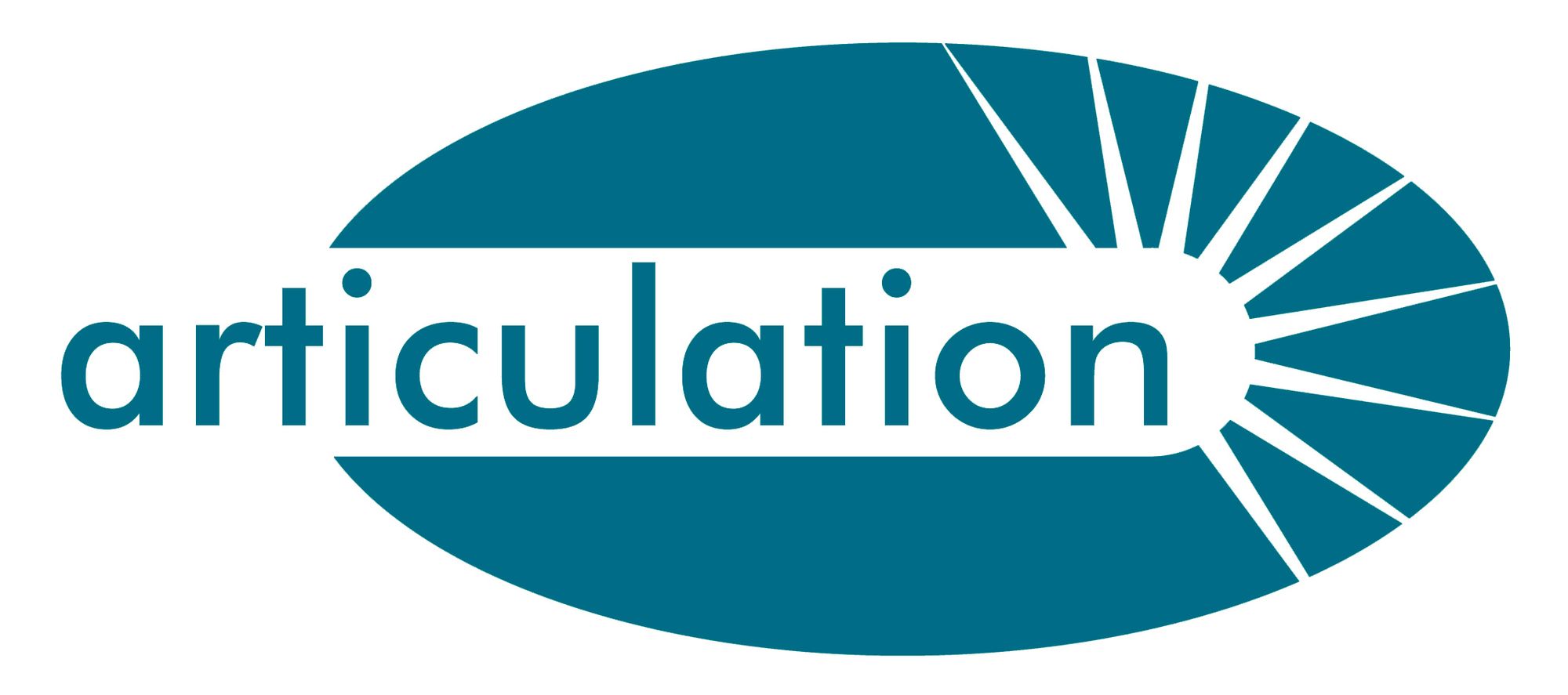
Funded by Creative Scotland
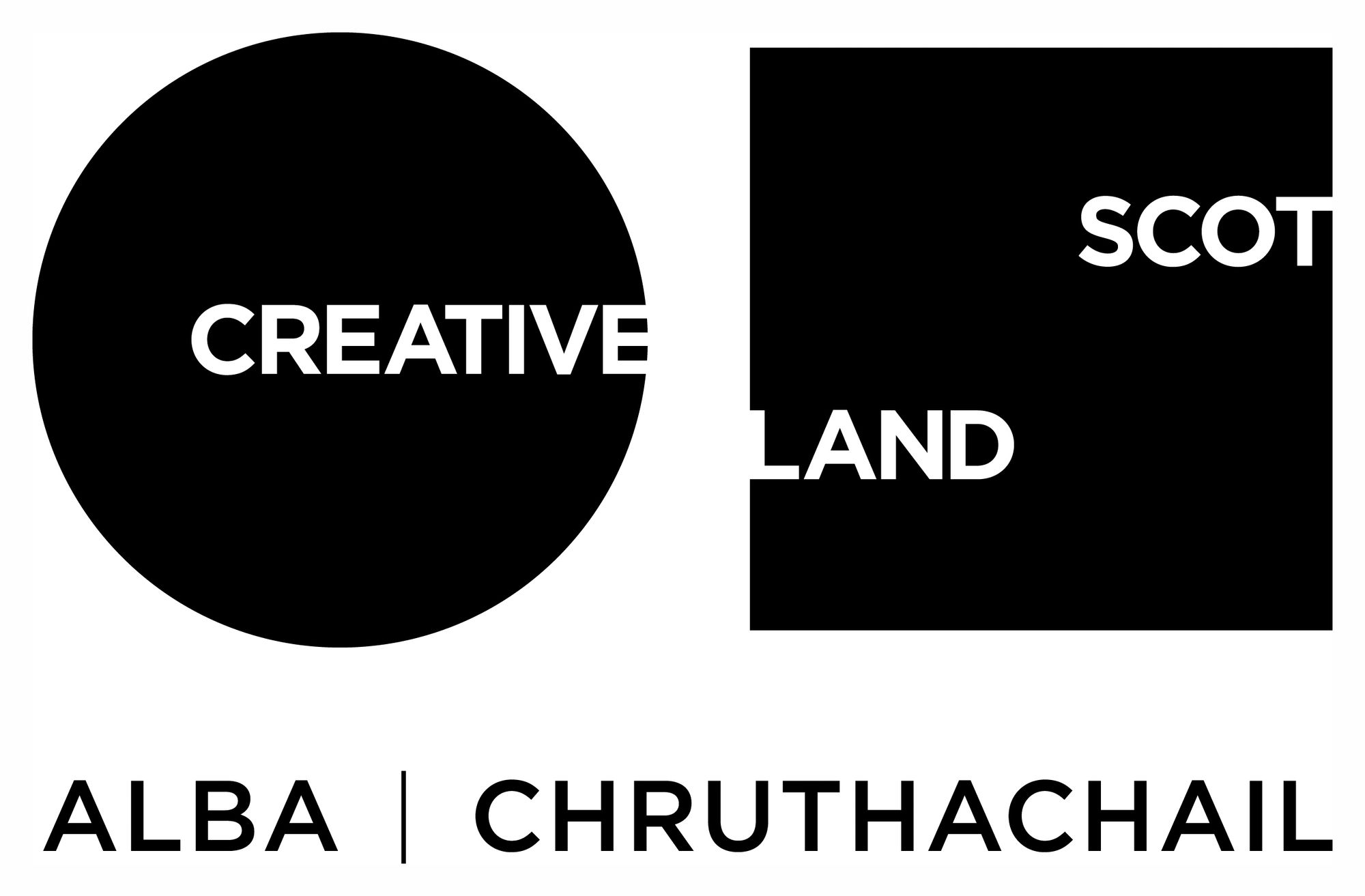